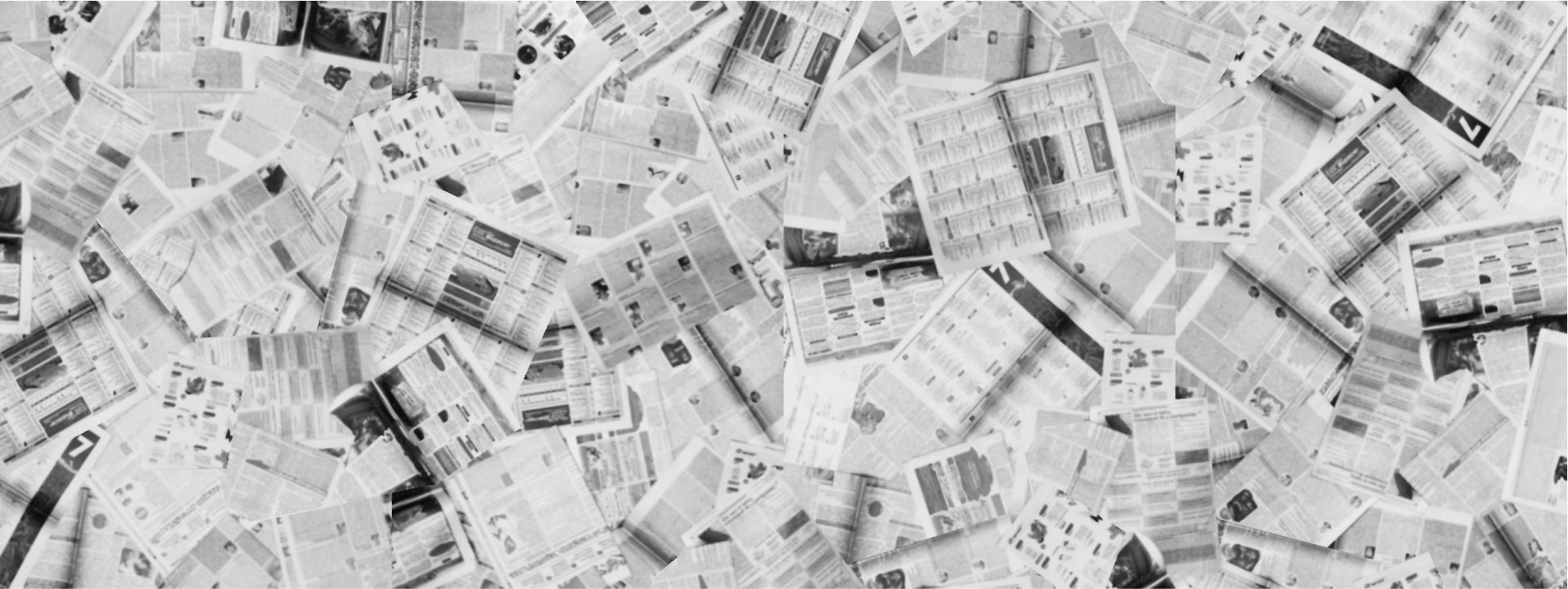
Download press release here
AIA Contract Documents and CERC announce partnership to help owners mitigate environmental risks.
Certified Environmentally Responsible Contractor (CERC), the leading pollution prevention certification, and AIA Contract Documents (ACD), provider of Industry Standard contract documents, have joined forces in a new partnership that offers CERC training to ACD customers at a discounted price.
With the growing importance of Environmental, Social and Governance (ESG), CERC recognizes contractors who train their employees to understand and mitigate the environmental risks associated with their business. ACD and Environmental Risk Professionals are partnering to offer resources created to help companies navigate ESG concerns.
“The certification program offered by Environmental Risk Professionals provides tools to implement safety training and qualification protocols as they pertain to environmental risks in ways that are not currently being addressed, but need to be,” said Chris Anderson, CEO at ACD. “Like ACD, CERC has helped business owners across the U.S. with their risk reduction and management strategy and our team is excited to build on that success and share these resources with our customers.”
The certification process includes a review of pollution insurance coverage to identify if a company has secured financial responsibility for a pollution event. Contractors must also commit to incorporating Pollution Prevention Practices within their safety culture to become certified.
The special price offering for ACD customers provides support to implement safety training and qualification protocols as they pertain to environmental risks in ways that are not currently being addressed. ACD Customers are encouraged to visit https://c-e-r-c.com/acd/ and participate in this opportunity.
“We are delighted to partner with AIA Contract Documents to provide a broad understanding of environmental risks facing the construction industry and raise awareness of the importance of hiring contractors that are trained and insured to mitigate the many environmental risks that are unique to each project,” said Darren Berg, President of Environmental Risk Professionals.
—-
About AIA Contract Documents
AIA Contract Documents is a digital platform that includes over 240 forms and contracts that define the relationships and terms involved in design and construction projects. Backed by the 135-year legacy of the American Institute of Architects, these comprehensive documents are widely recognized as the Industry Standard, and are used by all industry professionals, including architects, contractors, owners, consultants, and attorneys. Learn more at aiacontracts.com.
About Environmental Risk Professionals
Environmental Risk Professionals is an environmental consulting firm with a team of experienced experts determined to help companies minimize pollution claims. Environmental Risk Professionals helps businesses understand their risk exposures and in turn, mitigate potential claims and negative effects on the environment. The CERC certification program is administered by Environmental Risk Professionals. envriskpros.com
Carbon Capture
Carbon dioxide (CO2) is a greenhouse gas, which traps heat in the Earth’s atmosphere and contributes to climate change. Significant CO2 emissions are generated from various industrial sources, including refineries, electrical generation plants, cement manufacturing plants, etc., and studies have shown that global CO2 emissions must be cut by 50 to 80 percent by 2050 to avoid the worst impacts of climate change.[1] One of the methods to reduce CO2 emissions to the atmosphere is to capture the CO2 and store it underground, a process referred to as carbon sequestration.
As the effects of climate change, such as droughts, severe storms, and melting ice caps, become more evident, investors are putting pressure on publicly-traded companies to address climate change. For example, Exxon Mobil Corporation has recently leased approximately 500 thousand acres in the Gulf of Mexico near the coast of Texas, for a carbon sequestration project. In addition, another offshore drilling company, Talos Energy, is proposing to build a portfolio of four carbon sequestration projects along the Texas and Louisiana coasts.
According to an August 15, 2022 Reuters article[2], tax credits provided in the recent U.S. Inflation Reduction Act will help to make carbon capture projects more financially viable, providing up to $85 per ton for sequestering carbon dioxide produced by industry.
The process for carbon sequestration involves separating CO2 from air emissions generated by industry and energy sources, compressing the CO2 until it becomes a liquid, transporting it, and then injecting it into geologic units. Deep saline aquifers and oil and gas reservoirs, typically deeper than 800 meters, may be used for carbon sequestration.1 These formations consist of porous rock covered by an impermeable cap rock. Gas is injected into these units and is trapped there. The US Environmental Protection Agency (EPA) has designated the wells used to inject CO2 into deep rock formations as Class VI wells. In December 2010, the EPA issued the Federal Requirements Under the Underground Injection Control (UIC) Program for CO2 Geologic Sequestration Wells Final Rule, which established minimum technical criteria to protect underground sources of drinking water from the long-term subsurface storage of CO2.
Currently, the most common method of capturing CO2 from gas streams uses liquid solvents (such as amines). Other methods being studied include solid adsorbents, membranes, and cryogenic separation. Once the CO2 is separated, it is dried to remove water and compressed at high pressure into a dense fluid state, known as “dense phase” or “supercritical CO2”.[3] The preferred method for transport of the compressed CO2 is via pipeline. Once it reaches the storage site, it is injected by well into the formation.
There are a number of environmental risks associated with the different stages of carbon capture. High concentration exposures to CO2 can cause asphyxiation in humans, animals, and marine life and other contaminants can be released from carbon sequestration operations. The following presents some of the risks:
- Where liquid solvents are used to separate carbon from gas streams, these chemicals could be spilled during storage, use, and loading/unloading, resulting in contamination, bodily injury or property damage.
- Amines may be released as air emissions, and these can break down to more harmful substances in the atmosphere, which can have negative environmental effects, including health effects on humans, animals, plants, and the environment.
- Wastewater containing amines, amine degradation products, corrosion products, metals and/ other chemicals is generated when using amines in the capture process.[4] A reclaimer is used to capture amine solvent for reuse, and the wastewater generated from the reclaimer is considered to be a hazardous waste. Handling, storage, and loading/unloading of this waste could result in spills or leaks that impact the environment. Additionally, disposal of wastes at a third-party facility can result in tort liability related to the non-owned disposal facility, and transportation of wastes presents an environmental liability risk for the generator.
- At any point in separation, drying, or compression, there can be leaks of CO2, which can migrate into enclosed spaces and cause injury.
- Gases like carbon monoxide, hydrogen sulfide, nitrous oxide, water, sulfur dioxide, oxygen, and hydrogen may be present at small concentrations in CO2 and change the properties of the CO2 stream, with the most serious impact being corrosion of the piping system and potential failure.[5] Other pipeline defects could also result in leaks or releases of CO2.
- Damage to pipelines onshore could occur due to inadvertent damage during digging or due to vandalism or terrorism.
- Damage to offshore pipelines could occur due to anchor dropping or dragging by ships and result in a release.
- Injection wells can have blowouts. These can occur from equipment failures or over-pressurization of a well. Blowouts can release large volumes of CO2 and also drilling mud and debris can be ejected from the well, causing environmental damage.
- Leakage of CO2 and hydrocarbon gases (such as methane), which may also be present in the geologic formation, could occur from a geologic unit through an unplugged well or a fault or fracture in the overlying formation. The leakage of CO2 and hydrocarbon gases into a groundwater aquifer can contaminate the water source. Additionally, leakage could migrate to the surface and enter enclosed building spaces, which could harm human health, or be released to the air, which would pose risks to the global climate.
- Additionally,CO2 can displace saline water and well drilling or other carbon sequestration activities can create pathways for migration of saline water into a groundwater aquifer, degrading water quality in the aquifer.
According to Federal Regulation 40 CFR 146.85, the owner or operator of a Class VI injection well must demonstrate and maintain financial responsibility sufficient to pay for the following:
- Corrective action
- Injection well plugging
- Post injection site care and site closure
- Emergency and remedial response
One of the mechanisms that can be used to demonstrate financial responsibility, including liability and closure-related financial assurance, is insurance. Companies involved in any phase of the carbon sequestration operation need to financially prepare for short and long-term environmental risks. Pollution liability insurance may be available to manage financial risks and meet regulatory financial responsibility requirements. Companies should reach out to their insurance agent for more information on available policies.
CCP. “What Is CO2 Capture & Storage?” What Is CO2 Capture and Storage? , CO2 Capture Project, https://www.co2captureproject.org/what_is_co2_capture_storage.html.
Hampton, Liz. “Oil Industry Gears up to Tap U.S. Climate Bill for Carbon Capture Projects.” Reuters, Thomson Reuters, 15 Aug. 2022, https://www.reuters.com/markets/commodities/oil-industry-gears-up-tap-us-climate-bill-carbon-capture-projects-2022-08-15/.
[3]
Bellona. “Transport of CO2.” Bellona.org, 9 July 2015, https://bellona.org/about-ccs/how-ccs/transport-of-co2.
Shao, Renjie, and Aage Stangeland . “Amines Used in CO2 Capture - Health and Environmental Impacts.” Bellona Report, Bellona Network, Sept. 2009, https://network.bellona.org/content/uploads/sites/3/fil_Bellona_report_September_2009_-_Amines_used_in_CO2_capture.pdf.
Brown, A., et al. “Impacts: Framework for Risk Assessment of CO2 Transport and Storage Infrastructure.” Energy Procedia, Elsevier, 18 Aug. 2017, https://www.sciencedirect.com/science/article/pii/S1876610217319884.
Download press release here
Certified Environmentally Responsible Contractor (CERC) added as a special offering for Veriforce® supply chain risk management solutions.
Environmental Risk Professionals and Veriforce have announced that the companies entered into a partnership to leverage environmental resources and offer Certified Environmentally Responsible Contractor (CERC) certification at a discounted price to Veriforce customers through the Veriforce HUB.
CERC is a certification program that aims to promote environmentally responsible contractors by helping them stand out from lesser-qualified competition and win more bids. Darren Berg, president of Environmental Risk Professionals, points out how CERC benefits environmental, social, and governance (ESG) rating below:
Benefits of CERC
- Environmental
Pollution Prevention Practices and training specific to environmental issues can prevent environmental incidents, improve safety, and reduce wastes generated.
- Social
Having CERC certification shows the community that a company has considered the impact of their work on the environment and are leading the way toward environmental responsibility in the construction industry.
- Governance
Pollution liability insurance is complex, and pollutant definitions and coverages often vary between policies; therefore, pollution insurance is often not fully understood by insurance advisors. A CERC certificate demonstrates attention to detail to streamline the procurement process. It also shows how a company is protecting stakeholders through financial security for pollution conditions.
“Our team looks forward to helping Veriforce clients benefit from CERC certification. As part of the certification process, pollution liability insurance policies are verified for comprehensive pollution coverage. A CERC certificate can reduce the time project owners and general contractors spend verifying insurance requirements and demonstrate that a company has trained their employees on Pollution Prevention Practices,” Berg said.
Environmental Risk Professionals can support Veriforce’s commitment to helping their network of 50,000 contractors implement safety training and qualification protocols as they pertain to environmental risk in ways that are not currently being addressed.
“As part of our continued commitment to safety and added value in our solutions, partnering with Environmental Risk Professionals gives our clients an advantage in a time when ESG is a top priority.” Sandra Cashe, Chief Customer Officer of Veriforce, said.
Veriforce HUB members can request the CERC certification online at veriforcenetwork.com/cerc and receive the savings on this opportunity.
_____________________________________________________
About Environmental Risk Professionals
Environmental Risk Professionals is an environmental consulting firm with a team of experienced experts determined to help companies minimize pollution claims. Environmental Risk Professionals helps businesses understand their risk exposures and in turn, mitigate potential claims and negative effects on the environment. The CERC certification is administered by Environmental Risk Professionals. envriskpros.com.
About Veriforce
Veriforce® is a recognized leader in delivering comprehensive, integrated supply chain risk management solutions that help bring workers home safely and optimize business performance. Through a SaaS safety and compliance platform, data integrity and verification practices, and standardized safety training programs, Veriforce empowers leading organizations to drive safety and compliance into their supply chains and down to the worker-level. veriforce.com
DOWNLOAD PDF HERE
Dry Cleaner Bulletin
Dry cleaning dates back to ancient Rome. In the 1800s and early 1900s, petroleum-based products, such as gasoline, stoddard solvent and kerosene, were the primary solvents used in the dry cleaning process. However, due to their high flammability, they caused many fires and explosions, which resulted in injuries and casualties. Following World War I, chlorinated solvents were discovered and dry cleaning operations began to use them as their primary solvent for dry cleaning clothes. Perchloroethylene (PCE), also called tetrachloroethylene and PERC, has been the most commonly used dry cleaning solvent since the 1940s. It has been used in dry cleaning machines and for spot cleaning.
Over time, dry cleaning machines that use PCE as a solvent have evolved. Initial machines required operators to manually transfer cleaned fabrics from the washer to the dryer. The next generations of machines eliminated the requirement to transfer clothing and had the washing and drying process all in one unit, referred to as dry-to-dry. These early units often vented solvent vapors directly to the atmosphere. In the late 1970s and early 1980s, at a time when environmental regulations were being introduced, third-generation machines were developed with refrigerated condensers for vapor recovery. Fourth generation machines have both a carbon absorber and refrigerated condenser to recover additional solvent vapors. Fifth generation machines have the same features as fourth generation with the addition of controls to keep vapors below 300 parts per million (ppm) before the loading door can be opened. The 300 ppm concentration is the Occupational Safety and Health Administration’s ceiling limit for a single-exposure up to 5 minutes in any three-hour period.
The Environmental Protection Agency (EPA) has classified PCE as a likely human carcinogen. Exposure to PCE can irritate the eyes, nose and throat, and can cause headaches, dizziness, lightheadedness, nausea, vomiting, and fainting. It can affect the nervous system, liver, kidneys, reproductive system and can also harm fetuses.
In the environment, chlorinated solvents are highly mobile. Releases to the air may occur from storage, dry-cleaning machines, or during spot cleaning. Additionally, use of chlorinated solvents in dry cleaning establishments can result in spills and leaks that migrate to soil and groundwater. These chemicals can migrate through untreated concrete and even dissolve asphalt. Once in the environment, chlorinated solvents follow preferential pathways, such as coarse grain soils or utility corridors. They are denser than water (e.g., they sink) and are frequently present as dense non-aqueous phase liquids (DNAPLs) in the subsurface. Chlorinated solvents tend to migrate vertically deeper in groundwater until they reach impermeable or less permeable geologic units. Chlorinated solvents also easily volatilize into soil gas from contaminated soil or groundwater and can migrate from the subsurface into buildings to impact indoor air quality.
Historical practices at dry cleaners allowed drips and spills of solvent to occur. Equipment leaked onto the floor, which often wasn’t coated or protected. Fresh solvents may have been stored in aboveground or underground storage tanks and leaks occurred associated with loading/unloading and storage activities. Filters and solids removed from the cleaning and distillation process were often collected and stored outside a facility’s service door or on floors within the facility without containment. They also were disposed of in the municipal solid waste dumpster. Additionally, phase separated water from the dry cleaning machine was often disposed of on the ground outside of the dry cleaner or to sewers or septic systems. Although the phase separator equipment was intended to remove PCE, dissolved phase solvent remained in the water. The piping leading to sewer systems often leaked, discharging PCE to the subsurface. Additionally, discharges of solvent vapors would result in partitioning of PCE to underlying soil or condensation into liquids that dripped onto the ground.
While the use of chlorinated solvents at dry cleaners has become heavily regulated, pollution liability risks still exist. Use of older generation machines and equipment wear and corrosion can result in releases of solvent to the ground and as vapor to the atmosphere. Mishandling of solvents and wastes can still occur, resulting in additional releases. Air emissions within the dry cleaner can result in harm to workers (a workers compensation exposure) or to workers in adjacent retail and office spaces. Additionally, air emissions can migrate to adjacent properties leading to third-party claims. Chlorinated solvent releases to the subsurface can be extensive and difficult to remediate, resulting in potentially significant cleanup costs over long periods of time. Contaminated groundwater can migrate off-site to impact drinking water wells, surface waters, or indoor air, resulting in potential third-party cleanup, bodily-injury, property damage or natural resource damage claims. Dry cleaners establishments are also subject to “cradle to grave” liability under the Resource Conservation and Recovery Act (RCRA) for the hazardous wastes they generate from their operations. They could become liable for releases that occur during transportation of solvent wastes on their behalf. Additionally, they could become potentially responsible parties for cleanups at non-owned disposal sites where they have sent waste.
EPA has required the phase-out of PCE machines that are located in residential buildings by 2020 and implemented various controls and record-keeping requirements to limit air emissions related to PCE use. California took action against PCE use in dry cleaning when it banned the installation of any new PCE equipment after January 1, 2008. It also required that any PCE machines older than 15 years old must be placed out of service, and PCE is to be completely phased out for dry cleaning use in the state by 2023. Minnesota also passed a ban on the use of PCE as a dry-cleaning solvent starting in 2026. Some cities have also taken actions to reduce or eliminate the use of PCE. It is anticipated that additional actions may be taken at the state or federal level to limit the use of PCE by dry cleaners. Additionally, financial incentives have been provided in some states for dry cleaners to replace their machines with more eco-friendly machines. For example, in California, $10,000 grants have been given to dry cleaners who transition to liquid carbon dioxide or professional wet cleaning technologies. In Minnesota, the state has set up a $355,000 cost-share program to help dry cleaning businesses transition away from PCE use.
In addition to EPA and states working to further regulate or ban the use of PCE for dry cleaning, managing a dry cleaner’s pollution liability risk with insurance is becoming increasingly difficult. Many carriers are wary of providing coverage to dry cleaners that use PCE because there is a high potential for expensive cleanups and third-party claims related to dry cleaner operations. Many pollution carriers have chosen to not offer policies for dry cleaners, and others have implemented coverage restrictions or requirements to submit subsurface investigation data to obtain coverage.
Dry cleaners may consider switching out PCE for more environmentally friendly solvent alternatives. There are a number of alternatives to PCE that have been developed, including the following:
- High-flashpoint hydrocarbons use aliphatic hydrocarbons with flashpoints above 140°F. This is the most widely used alternative to dry cleaning with PCE. These solvents are less flammable than the hydrocarbon solvents used for dry cleaning in the early twentieth century, but they are more flammable than PERC.
- Water-based cleaning systems use water and detergents for cleaning. There are four types available: Professional wet cleaning systems, cold water cleaning systems, Green jet dry-wet cleaning systems and Green Dry-2-Dry systems. These use computer-controlled washers and dryers and specialized finishing equipment.
- Liquid carbon dioxide cleaning systems combine carbon dioxide with specialized detergents under high pressure.
- Acetal, or trade name SolvonK4, is a halogen-free combustible solvent.
- Propylene glycol ether is a class of combustible petroleum solvents that may be used in a hydrocarbon cleaning machine after making minor modifications.
- GreenEarth, a cyclic volatile methyl siloxane solvent, is an odorless, combustible liquid that may be used for cleaning.
- N-Propyl Bromide is a solvent that can be directly used with former PERC dry cleaning equipment; however, it is also toxic to humans and a possible human carcinogen.
Each of the above alternatives differs in its equipment costs, toxicity, persistence in the environment, impacts to human health, performance, etc.; however, in general changing to an alternative dry cleaning solvent has the following benefits:
- Your business may see more customers because people desire more “green” alternatives that will not leave residues or chemicals on the garments and other textiles they dry clean.
- As the public becomes more concerned about climate change and other societal issues, environmental, social and governance (ESG) factors are becoming more central to their decisions. Customers may be drawn to your business because it is more environmentally friendly.
- Switching to a PCE alternative can reduce the health risks to employees and reduce workers compensation premiums.
- Use of alternative solvents presents a reduced pollution exposure because other chemicals are not as mobile in the environment or as likely to present a vapor intrusion exposure if released to the environment.
- More options and cheaper pollution insurance alternatives may be available.
- The wastes generated from using dry cleaning solvent alternatives may be exempt from hazardous waste regulations, resulting in reduced disposal costs and less possibility of tort liability for disposal locations.
With an understanding that PCE presents a health risk to customers, workers, neighbors, and others; stricter regulations; and the significant pollution risks associated with its use, dry cleaners should look to alternative solvents for their businesses.
Download the PDF HERE
Per- and polyfluoroalkyl substances (PFAS) are man-made compounds that do not occur naturally in the environment. PFAS compounds are found in many products like carpet, upholstery, cookware, food packaging, and fire-fighting foam. Perfluorooctane sulfonate (PFOS) and perfluorooctanoic acid (PFOA) are fully fluorinated, organic compounds and two PFAS that have been produced in the largest amounts within the United States and most widely studied. The primary U.S. manufacturer of PFOS voluntarily phased out production of PFOS in 2002. In 2006, eight major companies in the PFASs industry voluntarily agreed to phase out production of PFOA and PFOA-related chemicals by 2015. Although many U.S. companies have stopped using PFOS and PFOA in their products, these PFAS compounds may still be present in foreign products that can be imported and sold in the U.S. Additionally, many other PFAS compounds are still used in manufacturing U.S. and foreign-made products.
According to the Environmental Protection Agency (EPA), PFAS have been found in the environment and in various products that people regularly use, including the following:
- In public and private drinking water wells.
- In soil and groundwater at or near landfills, disposal sites, and hazardous wastes sites.
- In aqueous film forming foam, which is used to extinguish Class B, flammable liquid fires. It was used in training and emergency response events at airports, shipyards, military bases, firefighting training facilities, chemical plants and refineries.
- In the air, soil or groundwater at manufacturing or chemical production facilities that produce or use PFAS.
- In food, such as fish in PFAS contaminated waters and dairy products where the livestock has been exposed to PFAS.
- In food packaging, such as grease resistant paper, fast food containers, etc.
- In stain and water-repellent coatings used on carpets, upholstery, clothing, cleaning products, non-stick cookware, etc.
- In personal care products, such as shampoos, dental floss, and cosmetics.
- In biosolids from wastewater treatment plants, which may have been applied to agricultural lands.
PFAS compounds are extremely persistent in the environment and resistant to typical environmental degradation processes primarily because the chemical bond between the carbon and fluorine atoms is extremely strong and stable. The following Table includes health effects identified in published studies for PFOA and/or PFOS (Source: Mueller, Robert. Human and Ecological Health Effects and Risk Assessment of Per-and Polyfluoroalkyl Substances (PFAS), Interstate Technology Regulatory Council (ITRC), https://pfas-1.itrcweb.org/wp-content/uploads/2020/10/human_and_eco_health_508_20200918.pdf.)
Table 1 - Health Effects From Exposure to PFOA or PFOS
The EPA indicates that people can be exposed to PFAS compounds in the following ways:
- Working in occupations that involve PFAS compounds, such as firefighting or chemical manufacturing or processing.
- Drinking PFAS contaminated water.
- Eating foods that contain PFAS.
- Swallowing contaminated soil or dust.
- Breathing air containing PFAS.
- Using products that are either made with or packaged in materials containing PFAS.
The Environmental Protection Agency (EPA) master list of PFAS contains thousands of structurally-defined compounds. Of those compounds, EPA is focusing their research on 37 based on their occurrence in the environment and potential health risks. The Unregulated Contaminant Monitoring Rule, passed on December 17, 2021, requires a representative number of public water systems of different sizes to monitor for 29 PFAS compounds. EPA collects nationally representative drinking water occurrence data to support future regulatory determinations and, as appropriate, assist in the development of national primary drinking water regulations.
In May 2016, EPA established drinking water health advisories of 0.07 micrograms per liter (µg/L) for the combined concentrations of PFOS and PFOA. According to the EPA’s PFAS Strategic Roadmap, a national primary drinking water regulation, in other words a Maximum Contaminant Level, is to be proposed for PFOA and PFOS by Fall 2022 and the Final Rule is expected to be issued in Fall 2023. However, various states have already established drinking water and groundwater guidelines for PFAS, which are listed in Table 2 below.
EPA has published draft recommendations for freshwater aquatic life Water Quality Criteria for PFOA and PFOS. Refer to the following webpage for more information on the proposed criteria:
https://www.epa.gov/wqc/aquatic-life-criteria-perfluorooctanoic-acid-pfoa
Additionally, on January 10, 2022, EPA proposed to designate PFOA and PFOS as hazardous substances under the Comprehensive Environmental Response, Compensation and Liability Act. The proposed rule gives EPA and other regulatory agencies the ability to require companies to perform remedial actions and to demand recovery costs from responsible parties.
According to the EPA, PFAS are found in people and animals all over the world. They are found in some food products and in the environment (air, water, soil, etc.). Completely stopping exposure to PFAS is unlikely. However, for people that live near sources of PFAS contamination there are steps that can be taken to reduce the risk of exposure to PFAS:
- Check with your state public health and environmental quality departments to learn if they have information regarding fish contaminated with PFAS and which types and local sources of fish that are safe to eat.
- If you find out that your water contains PFAS, use an alternative or treated water source for drinking, food preparation, cooking, brushing teeth, and any activity that might result in ingestion of water. Additionally, you can consider installing an in-home water treatment system to lower PFAS in your water.
- Routine showering and bathing are not a significant source of PFAS exposure, even when the water is contaminated with PFAS. Studies have shown very limited absorption of PFAS through the skin.
- Eat more fresh food at home, where you will be less likely exposed to PFAS containing food packaging. Do not store or reheat food in takeout food packaging. Do not microwave bags of popcorn.
--------------------------------------------------------------------------------------------------------------------------------------
About Environmental Risk Professionals
Environmental Risk Professionals is an environmental consulting firm with a team of experienced and committed experts determined to help companies minimize pollution claims. Through Pollution Prevention Practices, Operation and Maintenance Plans and other services, Environmental Risk Professionals helps businesses understand their risk exposures and in turn, mitigate potential claims and effects on the environment. Learn more about Environmental Risk Professionals by visiting envriskpros.com.
Molds are fungi that can be detected both indoors and outdoors year-round, and are found in virtually every environment. Warm, damp and humid conditions are ideal for mold growth. Outdoors they can be found in shady, damp areas or places where leaves or other vegetation is decomposing. Indoors they can be found where humidity levels are high, such as basements or showers.
Typical areas where mold is known to grow are places with a great deal of moisture, including leaks from roofs, windows and pipes, or areas susceptible to flooding. Mold grows well on paper products, cardboard, ceiling tiles and wood products. Mold can also grow in dust, paints, wallpaper, insulation, drywall, carpet, fabric and upholstery.
Whether hiring a contractor to complete construction activities at a job site or a contractor to complete mold abatement once growth has been detected, it is important for the contractor to be properly trained and insured. A lack of experience with mold prevention or abatement, and/or contractors with substandard or no insurance coverage for mold, can lead to inadequate abatement or future costly claims from mold exposure.
Project owners and general contractors looking to hire subcontractors with mold experience rely on contractor statements of qualifications and certificates of insurance to satisfy project requirements. However, standard certificates of insurance fail to confirm true pollution liability has been secured for a project and do not state if the pollution insurance is a Commercial General Liability (CGL) endorsement or a Contractors Pollution Liability (CPL) policy. A CGL endorsement typically has a pollution exclusion or an endorsement restricting coverage for mold and fungus, whereas a CPL policy covers environmental liabilities left uncovered by CGL policies with restrictive pollution exclusions. This is not evident just by reading the certificate of insurance.
______________________________
About Environmental Risk Professionals
Environmental Risk Professionals is an environmental consulting firm with a team of experienced and committed experts determined to help companies minimize pollution claims. Through Pollution Prevention Practices, Operation and Maintenance Plans and other services, Environmental Risk Professionals helps businesses understand their risk exposures and in turn, mitigate potential claims and effects on the environment. Learn more about Environmental Risk Professionals by visiting envriskpros.com.
Environmental legislation may hold parties liable for the contamination of a disposal site if a release was to be discovered at a later date, even if the waste had been properly disposed of at an approved disposal facility. All Commercial General Liability (CGL) policies contain some form of total pollution exclusion. Occasionally carriers are willing to give back limited coverage by endorsement; however, these endorsements do not typically address all risks. Among these excluded risks are Non-Owned Disposal Sites, leaving a contractor exposed. Contractors Pollution Liability (CPL) policies can provide coverage for hazardous waste disposed of at a properly permitted facility through Non-Owned Disposal Sites (NODS) coverage. If a disposal site has environmental problems, Federal, State and Local regulatory agencies may review the hazardous waste manifests and require all parties responsible for the disposal of the waste to pay for a portion of the cleanup.
NODS coverage is often written on a claims-made basis. Here are a few claim examples to consider that demonstrate the need for such coverage:
- An excavation contractor was responsible for a portion of the clean-up costs at a landfill after the discarded material was found to contain a variety of contaminants, including asbestos. Even though the contractor was unaware that the material was contaminated, the landfill filed suit against the contractor for improper classification and disposal of waste material.
- A construction company agreed to pay for improper disposal of PCBs in soils during a project. The contractor was responsible for excavating and disposing of contaminated material from the site, including 2,750 tons of material in an area with elevated PCB concentrations. According to the U.S. EPA, soils with lower concentrations of PCBs were mixed with soils containing higher concentrations, in violation of rules that do not allow dilution of contaminated materials. Some of the soil excavated contained PCB concentrations of 191 parts per million, more than seven times the 25-ppm concentration allowed at the disposal site where the mixed soils were sent for disposal.
- Called into a large renovation project, an electrician removed hundreds of old lighting fixtures and replaced them with new ones. The old ones were placed in 55-gallon drums and disposed of with the rest of the construction debris. A year later, the contractor was shocked to receive a letter from the EPA holding him responsible for over $1 million to clean up hazardous PCB's that were in the ballasts of the old fixtures and leaked from the drums, contaminating an otherwise sanitary landfill.
- An environmental contractor was hired by an environmental consultant to perform excavation, transportation and disposal of contaminated concrete and soil at a manufacturing plant. The excavated materials were segregated as non-hazardous and hazardous and placed into roll-off bin containers. The containers were then transported to either a hazardous or solid waste landfill in accordance with their waste profile. A few weeks later, as the consultant was finalizing their report a discrepancy between the consultant's notes and the waste disposal records revealed that a container of hazardous waste was incorrectly shipped to a non-hazardous waste landfill. During removal of the containers from the site, the contractor mixed up two containers of broken concrete and inadvertently transported hazardous waste to a non-hazardous waste landfill. Due to the time that had passed between the discovery of the mistake and disposal date, the landfill had estimated the material was buried under at least 60 feet of waste, and the likeliness of finding it was very slim. A risk assessment was required by the state environmental agency and the manufacturing plant was fined for improper disposal of hazardous waste. The manufacturing plant sued the environmental consultant, who then sued the environmental contractor to recoup costs associated with the fine and legal fees.
Project owners and general contractors generally rely on a contractor’s statement of qualifications and certificates of insurance to satisfy project requirements. However, standard certificates of insurance fail to confirm true pollution liability has been secured for a project and do not state if the pollution insurance is a Commercial General Liability (CGL) endorsement or a Contractors Pollution Liability (CPL) policy. A CGL endorsement typically has a pollution exclusion or an endorsement restricting coverage for NODS, whereas a CPL policy covers environmental liabilities left uncovered by CGL policies with restrictive pollution exclusions. This is not evident just by reading the certificate of insurance.
__________________
About Environmental Risk Professionals
Environmental Risk Professionals is an environmental consulting firm with a team of experienced and committed experts determined to help companies minimize pollution claims. Through Pollution Prevention Practices, Operation and Maintenance Plans and other services, Environmental Risk Professionals helps businesses understand their risk exposures and in turn, mitigate potential claims and effects on the environment. Learn more about Environmental Risk Professionals by visiting envriskpros.com.
Pollution claims are often costly and challenging to handle. The lower the limits of insurance, the greater the risk of being underinsured and having to pay for a cleanup out of pocket. Cleanups of environmental pollution incidents can be very expensive and time-consuming. Commercial general liability (CGL) insurance policies all have a set limit, which is the most the policy will pay on behalf of its named insured. If a contractor decides to add a pollution endorsement to their CGL policy, the limits are generally shared with the CGL. This means frequency-driven CGL claims can reduce limits. A standalone pollution policy adds a deeper level of protection to an insured by securing financial responsibility for a pollution event.
The following claims examples demonstrate how quickly environmental losses can add up:
- Fifteen students and teachers suffered mild to severe injuries when a faulty HVAC system circulated carbon monoxide and fireproofing chemicals in their school over an extended time period. Some experienced temporary respiratory illnesses; however, one student required a lung transplant and has a shortened life expectancy. Actual settlement damages totaled several million dollars and were to be paid by the school district and the HVAC system designer and installer.
- A general contractor was responsible for overseeing the renovation of a hospital wing. When two patients died in the intensive care unit adjacent to the construction zone, the contractor was sued for inadequate monitoring and containment of the construction zone. The patient's cause of death was determined to be an organic fungus found in the ventilation system and traced back to dust generated during renovation activities in the construction zone. The contractor was responsible for $10 million in damages.
- An industrial contractor dropped a 30-ton piece of equipment from a crane onto a pipe leading to a hydrofluoric acid tank. Acid was emitted into the surrounding atmosphere, creating a vast vapor cloud. Approximately 3,000 residents were evacuated and 1,000 were treated for respiratory injuries. The court entered judgment, holding the contractor 95 percent liable for the accident. To date, 4,500 claims have been filed in excess of $23 million. The claims include bodily injury, property damage, lost profits and emergency response costs.
- One landscaping contractor was hired to control weeds and vegetation in a residential neighborhood surrounding a golf course. Overapplication resulted in chemicals impacting the lake in the middle of the golf course. Lake water was then used on the golf course, and the grass on all 18 holes was impacted. It was estimated that 8-10 inches of topsoil on the entire golf course needed to be removed, costing several million dollars.
- A contractor installed a liner at a gypsum stack. Gypsum stacks are phosphogypsum piles originating from the processing of phosphate rock that contains small amounts of radionuclides. The liner subsequently leaked. The contractor was obligated to contribute $1 million towards the $15 million cleanup of a neighboring waterway. $4 million in defense expenses were incurred to get to settlement.
- An excavation contractor was retained to remove and dispose of contaminated soil at a construction site. They were told by the City that the utilities had all been shut off prior to the work commencing. During excavation, they hit a water main that was supposed to be inactive. Upon impact, the water main released over a million gallons of water and contaminated soil into a city street. The water was eventually shut off, and the city street was shut down overnight to accommodate the cleanup. The clean-up costs totaled $3.4 million, including the cost of the emergency response measures.
Project owners and general contractors generally rely on a contractor’s statement of qualifications and certificates of insurance to satisfy project requirements. However, standard certificates of insurance fail to confirm true pollution liability has been secured for a project and do not state if the pollution insurance is a Commercial General Liability (CGL) endorsement or a Contractors Pollution Liability (CPL) and Transportation Pollution Liability (TPL) policy. A CGL endorsement typically has a pollution exclusion or an endorsement restricting coverage, whereas a CPL/TPL policy covers environmental liabilities left uncovered by CGL policies with restrictive pollution exclusions. This is not evident just by reading the certificate of insurance.
______________________________
About Environmental Risk Professionals
Environmental Risk Professionals is an environmental consulting firm with a team of experienced and committed experts determined to help companies minimize pollution claims. Through Pollution Prevention Practices, Operation and Maintenance Plans and other services, Environmental Risk Professionals helps businesses understand their risk exposures and in turn, mitigate potential claims and effects on the environment. Learn more about Environmental Risk Professionals by visiting envriskpros.com.
The General Building Contractors Association provides recommended COVID-19 job site protocols for social distancing, personal responsibility, sanitation and disinfection, office and jobsite, visitors, and personal protective equipment. Although the implementation of these protocols can assist employers with preventing the spread or transmissions of COVID-19, some may create unintentional issues for contractors. For example, one protocol suggests that employers discontinue the use of water coolers and provide individual water bottles to workers or instruct them to bring their own. This may create several issues with some employers, including the following:
- Use of single-use water bottles creates added waste and is counter to many contractors’ efforts to be greener and more environmentally conscious.
- Use of single-use water bottles may create housekeeping issues at jobsites if they are not properly disposed of in waste receptacles or placed in recycling bins.
- Recent supply-chain issues have resulted in delays and shortages of single-use water bottles.
- Supplying single-use water bottles in lieu of a common water cooler creates an added cost for contractors.
Other sources reviewed, including the Center for Disease Control (CDC), do not specify that the use of common water coolers be suspended or discontinued. In fact, the heat-related illness prevention page for CDC recommends steps employees can take to minimize their risks for COVID when using a common water cooler. According to the CDC, a common water cooler can be used with precautions. The following protocols can be used to reduce the risk of COVID spread while using a common water cooler:
- Post a sign to encourage handwashing, physical distancing, and use of masks while refilling water.
- Provide a handwashing station, alcohol-based hand sanitizer with at least 60 percent ethanol or 70 percent ethanol, disinfectant wipes and/or disinfectant spray from the U.S. Environmental Protection Agency (USEPA)
- list of approved products for use against COVID-19 and paper towels.
- Post signs to clean before and after using shared surfaces at the water cooler.
- Provide a lined trash bin for disposal of paper towels.
- Consider a touch-free water cooler.
- Place visual cues such as taped or painted lines, rocks, stakes, or signs at the watering point to show where people should stand at least 6 feet from each other when waiting for water.
- Provide refillable drinking bottles to employees with their names already printed on them.
- Have an extra supply on hand of disposable cups or paper cones.
- Post signs and remind employees to avoid touching their bottle, cone or cup to the water dispenser when refilling it.
- Clean water cooler handles frequently with USEPA approved disinfection products.
________________________________
About Environmental Risk Professionals
Environmental Risk Professionals is an environmental consulting firm with a team of experienced and committed experts determined to help companies minimize pollution claims. Through Pollution Prevention Practices, Operation and Maintenance Plans and other services, Environmental Risk Professionals helps businesses understand their risk exposures and in turn, mitigate potential claims and effects on the environment. Learn more about Environmental Risk Professionals by visiting envriskpros.com.
According to the National Safety Council (NSC), the Occupational Safety and Health Administration (OSHA) just released preliminary information on which safety exposures resulted in the highest numbers of violations issued by their department this year. Respiratory protection violations ranked second highest on the OSHA violations list. According to OSHA’s Director of Enforcement, Patrick Kapust, who presented the list at the 2021 NSC Safety Congress & Expo, the number of violations for respiratory protection were higher than usual this year due partially to health-care related violations related to the COVID-19 pandemic; however, a number of respiratory protection violations were issued to companies in industries where silica exposure is a concern.
According to OSHA, respirable crystalline silica is generated by high-energy operations like cutting, sawing, grinding, drilling and crushing stone, rock, concrete, brick, block and mortar; or when using industrial sand. Once inhaled, silica accumulates in the lungs and causes lung inflammation, which leads to scarring and formation of nodules, called silicosis, a type of pulmonary fibrosis. Exposure may lead to silicosis, chronic obstructive pulmonary disease (COPD), lung cancer, or kidney disease.
Construction workers, factory employees, and third-parties can be exposed to silica during construction or manufacturing operations if engineering controls and safe work practices are insufficient or inadequate. Injured workers may seek compensation from their employers through a workers compensation claim. However, workers and other parties may also sue manufacturers of silica-based products seeking compensation through a product liability lawsuit. People who are exposed to silica through operations by others may also file lawsuits for bodily injury.
General liability policies may not cover product liability or third-party bodily injury claims resulting from silica exposure because these policies often carry “total pollution exclusion” endorsements. Silica would be considered a pollutant because federal regulations consider it to be an air contaminant. Therefore, those companies at risk for silica related exposure claims should consider the purchase of a pollution liability insurance policy to protect their financial interests.
In November 2021, The California State Regional Water Quality Control Board (SRWQCB) published a pamphlet titled Draft Microplastics in Drinking Water Policy Handbook that sets requirements for drinking water monitoring and reporting for microplastics. The policy was developed after California passed a law in 2018 that required testing for microplastics in drinking water to establish safe drinking water limits. The policy requires monitoring of source waters and treated drinking water. Source waters will be monitored initially and then drinking water in the second phase. By monitoring its presence in the environment, scientists can better understand the prevalence and health risks to humans.
What are microplastics? The SRWQCB defines microplastics as follows:
“Solid polymeric materials to which chemical additives or other substances may have been added, which are particles which have at least three dimensions that are greater than one nanometer (nm) and less than 5,000 micrometers (μm).”
Natural polymers, which are those that haven’t been chemically altered, are excluded. ‘Polymeric material’ means either (i) a particle of any composition with a continuous polymer surface coating of any thickness, or (ii) a particle of any composition with a polymer content of greater than or equal to 1% by mass. One type of microplastic is called a nurdle, which are tiny beads that are the basic raw material in manufacturing plastic products. They are made from polyethylene, polypropylene, polystyrene, polyvinyl chloride, or other plastics, along with different additives for some nurdles. Other microplastics are broken down and released from plastic products.
According to the Ocean Blue Project’s article, A Deep Dive into Plastic Pollution, eight tons of plastic enters oceans on a yearly basis (Cuddapah, 2021). What’s more, a report from The Guardian states that approximately 230,000 tons of nurdles end in oceans every year (McVeigh, 2021). Plastics are highly persistent and can take decades to degrade naturally. The surfaces of nurdle pellets reportedly absorb chemical toxins and other pollutants. Studies, such as Jiana Li’s study, titled Using Mussels as a Global Bioindicator of Coastal Microplastic Pollution, have also shown that nurdles can act like a raft, facilitating colonization of bacteria, like cholera and e-coli, which may be present in surface waters from wastewater discharges.
A recent high profile spill of nurdles occurred in May 2021 when the X-Press Pearl container ship caught fire and sank near Sri Lanka’s coast. The United Nations (UN) classified the accident as Sri Lanka’s “worst maritime disaster” because of the 1,680 tons of nurdles that were released (McVeigh, 2019). Reportedly, billions of nurdles and dead turtles, fish, whales, and dolphins with nurdles in their bodies washed up on Sri Lanka’s beaches.
Several studies have shown possible toxicity in the human body from microplastics. Arifur Rahman’s study, titled Potential Human Health Risks Due to Environmental Exposure to Nano- and Microplastics and Knowledge Gaps, highlights this toxicity and the effects it has on one’s health, including disruption to the digestive system and the nervous system and increased risk of cancer (Rahman, 2020) The World Health Organization (WHO) concluded in 2019 that more research is needed to understand microplastics’ impacts on human health.
Accountability and toxic tort related to microplastics could be expansive if they are found to be harmful to humans. Manufacturers of nurdles and plastic products may be at the center of suits; however, companies that use plastics in their products, wastewater treatment facilities, and many other entities could be drawn into lawsuits. Risk managers should take the potential liability related to microplastics into consideration and prepare their companies accordingly. One option to evaluate is to consider pollution liability insurance as a risk transfer mechanism.
__________________________________________________________
References
Cuddapah, Arpita. “A Deep Dive into Plastic Pollution.” Ocean Blue Project, Ocean Blue Environmental News Blog, 5 Aug. 2021, https://oceanblueproject.org/can-we-survive-without-the-ocean/.
Li, Jiana, et al. “Using Mussels as a Global Bioindicator of Coastal Microplastic Pollution.” Environmental Pollution, vol. 244, 2019, pp. 522–533., https://doi.org/10.1016/j.envpol.2018.10.032.
McVeigh, Karen. “Nurdles: The Worst Toxic Waste You’ve Probably Never Heard Of.” The Guardian, Guardian News and Media, 29 Nov. 2021, https://www.theguardian.com/environment/2021/nov/29/nurdles-plastic-pellets-environmental-ocean-spills-toxic-waste-not-classified-hazardous.
Rahman, Arifur, et al. “Potential Human Health Risks Due to Environmental Exposure to Nano- and Microplastics and Knowledge Gaps: A Scoping Review.” Science of The Total Environment, vol. 757, 2021, p. 143872., https://doi.org/10.1016/j.scitotenv.2020.143872.
Fires have environmental impacts that can affect air, soil and water quality. The combustion of building materials or chemicals stored at a facility can cause harmful constituents to be emitted to the atmosphere or carried with water or foams used to fight the fire into the surrounding environment. If you are relying on a property policy or commercial general liability policy to protect your company financially in the event of a fire, you may be caught off guard. These policies are not likely to provide adequate coverage if a pollution event occurs as a result of a fire.
Recently, an explosion and fire at a chemical plant that manufactures lubricants, grease products, and other fluids, caused extensive damage to the environment. A half a million gallons of lubricating oils were stored at the facility, along with lead, antifreeze, nitrogen, sulfuric acid, and other hazardous chemicals. The fire caused the evacuation of residents within a one-mile radius of the facility, and individuals within a three-mile radius of the facility were asked to wear masks. Fire-related debris drifted onto yards and surfaces of nearby properties. A river, which is a groundwater source for the community, is located approximately 600 feet from the facility. Initially, water was applied on the fire, but crews ceased applying water when authorities became concerned with the potential run-off of contaminated water into the river. A private contractor was subsequently hired by the chemical plant to help extinguish the fire. The contractor initially used aqueous film fighting foam (AFFF) containing per- and polyfluoroalkyl substances (PFAS). PFAS are described as “forever chemicals” because they are persistent and don’t readily break down over time. After approximately three hours, the use of PFAS containing AFFF was halted due to the concern over PFAS, and steps were taken to contain the runoff. However, PFAS and chemicals released from the plant could have seeped into the soil and groundwater.
The chemical company faces a myriad of losses and potential third-party claims from this fire, including the following:
- Damage to on-site structures and equipment
- Damage to other on-site property like foundations, landscaping, parking lots, etc.
- Business interruption
- On-site pollution cleanup
- Off-site pollution cleanup
- Third-party bodily injury and property damage claims
- Third-party business interruption claims
- Natural resource damage claims
- Non-owned disposal site liability risks for debris and wastes generated ` from the fire and any resulting pollution
- Transportation of wastes and debris from the site to a disposal site
Insurance Considerations
Property policies will only provide coverage for direct physical loss or damage caused by a covered cause of loss. Fire would be one of those covered causes of loss on all property policies, and direct damage and debris removal for covered property, such as facility buildings, would be covered. However, what if run-off from firefighting techniques contaminated parts of your facility such as the foundation and the parking lot, and these need to be demolished and removed in conjunction with a cleanup? These “other structures” typically are either not covered by a property policy or have low sublimits of coverage. Therefore, the cost for debris removal for these parts of your property would not be covered. Most property policies provide some coverage for a pollutant release caused by a fire; however, most policies have a limit of $10,000 to extract pollutants from water and land, and this amount is unlikely to be sufficient if a large fire occurs and results in contamination to soil, groundwater, or surface waters.
Business interruption may be covered under a Business Income (and Extra Expense) Coverage Form; however, the trigger for coverage would be direct damage to the building. What if governmental authorities require monitoring, investigations, or remediation that extend the length of a business’s closure? The added business interruption losses caused by the governmental order would not likely be covered.
Commercial General Liability (CGL) policies provide coverage for third-party liability claims. However, the International Organization for Standardization (ISO) CGL form contains an “absolute pollution exclusion.” A “hostile fire” exception exists in many policies, which applies to bodily injury or property damage arising from heat, smoke, or fumes from a “hostile fire”, but some insurers will replace the “absolute pollution exclusion” with a more restrictive exclusion that does not include the hostile fire exception. For the previously discussed chemical facility fire, bodily injury or property damage caused by fumes, smoke, etc. from the fire may or may not be covered under the company’s CGL policy, depending on the coverage language. For any of the contamination caused by releases of chemicals from within the facility, spread by water used on the fire, or from the foam used to extinguish the fire, the company’s CGL policy would not cover or would limit the coverage for cleanup expenses on-site or off-site. It would not cover third-party bodily injury or property damage claims resulting from the contamination itself. For example, if the PFAS chemicals present in the fire-fighting foam contaminate the groundwater, and the groundwater migrates to a neighbor’s property, impacting the quality of their well water, then the company would not be covered from claims by the neighbor related to their well for property damage. Furthermore, if any of the chemicals or run-off from fire-fighting efforts migrate to the river and impact the aquatic environment or water quality, then Natural Resource Damage (NRD) claims could be brought against the chemical company, which a CGL policy would not cover. Furthermore, third-parties whose businesses are impacted by having to evacuate may also file claims for their business losses against the property owner who had the fire. A carrier may deny coverage for these losses, depending on the circumstances and language of the CGL policy.
Wastes are generated from debris removal, fire response, response efforts, monitoring, investigations, or remediation at the location of a fire. Some of these wastes may be characterized as hazardous wastes. The property owner has “cradle to grave” liability for any wastes generated at his property. Therefore, if a non-owned disposal facility where these wastes are taken ever had a release, the property owner could become a Potentially Responsible Party (PRP) in the cleanup of that third-party non-owned disposal site. Additionally, while these wastes are being transported, if an accident occurs that results in a release, then the property owner could become liable for cleanup or third-party claims related to the over-the-road release.
Conclusion
While this chemical plant fire presents a catastrophic case, any business that stores or handles chemicals needs to be prepared for the potential pollution losses from a fire. If your company is relying on property and CGL policies to help financially recover from the devastating losses caused by a fire, you may be leaving yourself open to significant gaps in coverage. Cleanup, third-party claims, and natural resource damages related to pollution caused by a fire may only be partially covered or not covered at all. Non-owned disposal site and transportation-related pollution risks would also not be covered. Therefore, obtaining a separate Pollution Liability Insurance policy, which would provide the excluded coverages indicated above, is a prudent risk management decision to protect your company.
About Environmental Risk Professionals
Environmental Risk Professionals is an environmental consulting firm with a team of experienced and committed experts determined to help companies minimize pollution claims. Through Pollution Prevention Practices, Operation and Maintenance Plans and other services, Environmental Risk Professionals helps businesses understand their risk exposures and in turn, mitigate potential claims and effects on the environment. Learn more about Environmental Risk Professionals by visiting envriskpros.com.